Jak informowaliśmy w pierwszej części poradnika, mieszalniki możemy sklasyfikować według różnych kryteriów. Ze względu na przeznaczenie wyróżniamy mieszalniki dla przemysłu chemicznego, kosmetycznego, spożywczego i farmaceutycznego. Urządzenia te można również podzielić ze względu na budowę oraz rodzaj mieszadła, a także na ciśnieniowe i bezciśnieniowe.
Podział ze względu na budowę
Mieszalniki mają rozmaite przeznaczenie, dlatego różnią się konstrukcją i zastosowaną w nich technologią. Biorąc pod uwagę budowę urządzeń można wyróżnić:
- mieszalniki jednopłaszczowe,
- mieszalniki dwupłaszczowe,
- mieszalniki trójpłaszczowe.
Mieszalniki jednopłaszczowe to na ogół proste konstrukcje, które składają się przede wszystkim ze zbiornika oraz mieszadła. Zbiornik składa się wtedy tylko z jednej przestrzeni roboczej.
Mieszalniki jednopłaszczowe mogą być stosowane w wielu miejscach, np. w przemyśle kosmetycznym, spożywczym a także farmaceutycznym. Jednak w przypadku bardziej zaawansowanych procesów technologicznych wskazane jest użycie również bardziej złożonych urządzeń.
Mieszalniki dwupłaszczowe wyglądają podobnie, jak jednopłaszczowe. Wyróżniają się jednak dodatkową warstwą izolacji. Rolę izolatora może pełnić wełna mineralna lub pianka poliuretanowa. Jest on zabezpieczony od zewnątrz blachą kwasoodporną.
Dodatkowy płaszcz sprawia, że zwiększają się możliwości wykorzystania mieszalnika. Urządzenie dłużej może utrzymywać stałą temperaturę, co ma szczególne znaczenie w niektórych gałęziach przemysłu.
Najbardziej zaawansowane pod względem konstrukcyjnym są mieszalniki trójpłaszczowe, które ze względu na wysoki stopień bezpieczeństwa mogą być stosowane do mieszania wielu substancji również pod wysokim ciśnieniem. Wyróżniają się tym, że – w porównaniu z mieszalnikiem dwupłaszczowym – posiadają dodatkowy płaszcz grzewczo-chłodzący.
Płaszcz grzewczo-chłodzący może być wykonany w formie kanałów bądź też w formie pillow plate. Pillow plate składa się z dwóch arkuszy blach ze stali nierdzewnej, które są ze sobą punktowo spawane w wielu miejscach. Dodatkowo obrys zewnętrzny arkuszy jest spawany w sposób ciągły, zapewniając szczelność.
Powstałą w ten sposób konstrukcję wypełnia się wodą, olejem termicznym czy też np. glikolem. Tego rodzaju ciecz pełni rolę medium przewodzącego ciepło lub zimno. Płaszcz ten przypomina wyglądem poduszkę, która, choć jest stosunkowo lekka, ma bardzo dobre właściwości termo-hydrauliczne.
Podział ze względu na mieszadła
Mieszanie cieczy może odbywać się mechanicznie, pneumatycznie, hydraulicznie, a nawet poprzez zastosowanie ultradźwięków. Najczęściej jednak stosuje się metodę mechaniczną za pomocą mieszadeł. Dlatego podział mieszalników przemysłowych zależy również od rodzaju mieszadeł, a co za tym idzie charakteru cyrkulacji substancji. W takim przypadku wyróżniamy następujące rodzaje mieszalników:
- generujące okrężny przepływ substancji – mają one np. mieszadła kotwicowe lub skrobakowe,
- tworzące promieniowy przepływ substancji – np. mieszalniki łopatowe ze stali lub turbinowe.
Mieszadła dzielą się również ze względu na szybkość obrotu oraz intensywności mieszania na:
- mieszadła wolnoobrotowe – ramowe, kotwicowe, wstęgowe – stosowane najczęściej w przypadku substancji o dużej lepkości,
- mieszadło szybkoobrotowe – śmigłowe i tarczowe, które stosuje się przeważnie do przyspieszenia reakcji chemicznych czy ujednolicenia substancji.
Odpowiednie dopasowanie mieszadeł do procesu jest niezwykle ważne. Pozwala uzyskać zaplanowaną substancję w możliwe najkrótszym czasie minimalizując również zużycie energii elektrycznej.
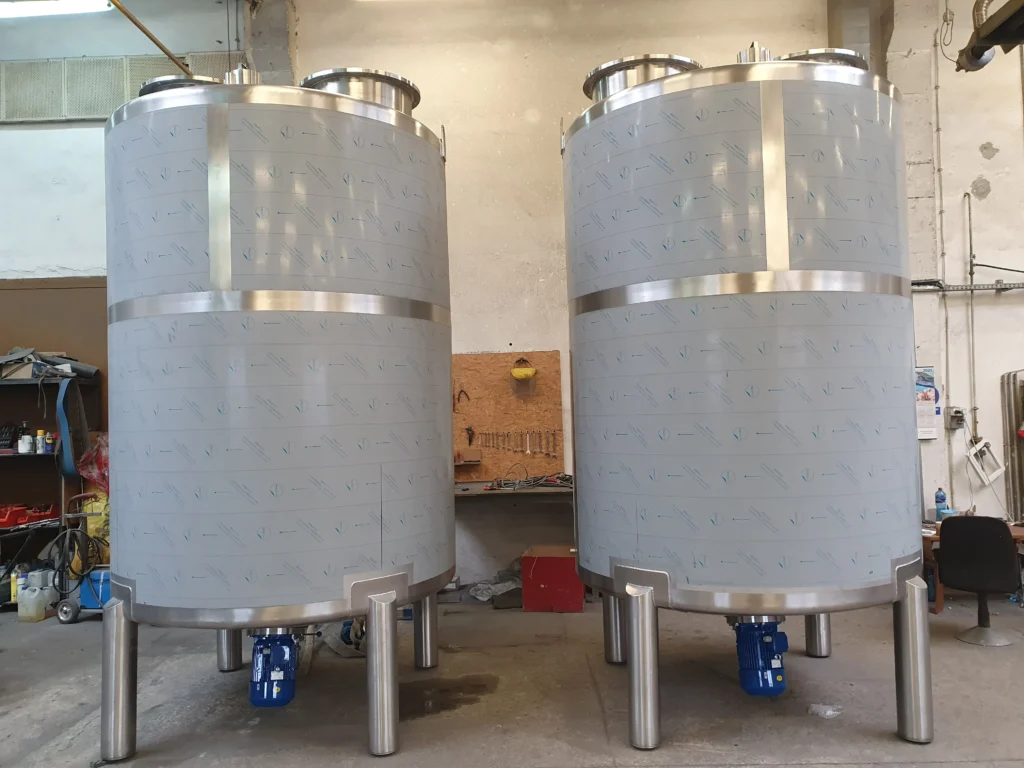
Mieszalniki ciśnieniowe i bezciśnieniowe
Kolejnym kryterium klasyfikacji jest podział mieszalników ze względu na ciśnienie. W tym przypadku rozróżniamy:
- mieszalniki bezciśnieniowe,
- mieszalniki ciśnieniowe.
Mieszalniki bezciśnieniowe to na ogół proste maszyny z mieszadłem i podstawowym systemem sterowania.
Z kolei mieszalniki ciśnieniowe to zdecydowanie bardziej zaawansowane konstrukcje. W zależności od potrzeb mogą one posiadać płaszcz grzewczy, zespół mieszadeł czy automatyczne systemy sterowania.
Wykwalifikowani konstruktorzy BIES są w stanie stworzyć mieszalnik o dowolnej konfiguracji, który będzie odpowiadał wymaganiom konkretnego procesu.